ケースの製作について
(ネタバレ含む)
1. 試作
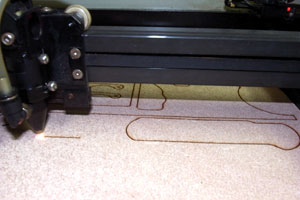
CADで設計をして、レーザーで一回一回革を切って、組み立て、CADのデータを調整して〜という行程を何度も繰り返し(平均20回ぐらい試作)、これ以上直すデータがないというぐらいまで詰めたところで、刃型の発注をいたします(2009年6月現在、刃型は特に複雑なもの以外はほぼ内製で行っております)。
刃型の精度は+-0.3mmぐらいですので、ちょっとぐらいいい加減なデータでも良いような気がしますが、いい加減なデータを元に作ると、やはりいい加減な寸法の刃型が出来上がるので、レーザー加工機で0.05mm単位でデータを調整いたします。
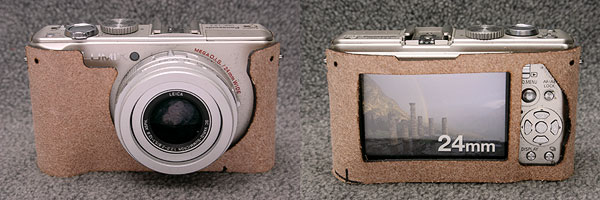
上の画像は、試作9号ぐらいです。あと10回は試作しないと、きちんとした形が決まらないです。
上の写真はGX200の打ち抜き刃型の写真です。複雑な曲線が組み合わさった形状で、革包丁で切り出していたら、1時間かかるような代物です。刃型があれば、カットは数秒です。1000枚切っても1000枚とも寸分違わないサイズでカットできます。製品としてきちんとしたケースを作るのは、刃型がないと正直話になりません。
刃型が出来上がったら、製品試作をいたします。だいたい10個ぐらいです。製品試作でダメ出しをしたり、行程を最適化したりします。
2.製造の最適化
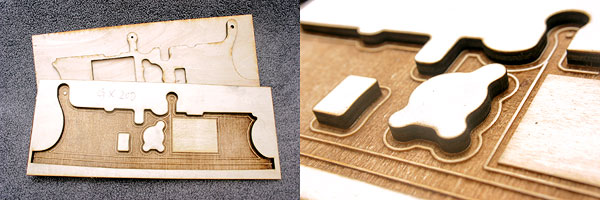
生産行程の最適化は準備に手間と時間がかかりますが非常に大切なことです。
上の写真はGX200の裏革と表革を貼り合わせるときに使う型枠です。表革を枠に入れて、接着剤を塗って貼り合わせ、上からプレス機で圧着いたします。
革の貼り合わせなど簡単なことのように思えますが、形がすでに決まっているものをズレることなく貼り合わせるということは、実は非常に難しい作業です。型枠があると熟練を必要とせず、誰でもきちんと端と端を合わせて貼り合わせることが出来ます。
圧着することによって上の写真にある細い線が表革にエンボス状に入ります(ネンと言います)。このネンがステッチラインとなります。つまりこのネンに沿ってミシンを走らせれば、ステッチラインが揃います。
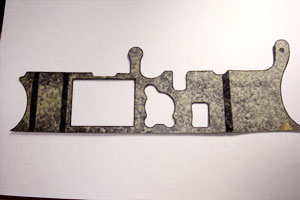
小さなコンパクトデジカメの場合、薄い革を使いますので、形状を保つためフレームを入れる必要が出てきます。
上の写真はGX200ケースの裏革とフレームの写真です。
フレームは、革の端と曲がり部分は必要ありませんので、すべての革の端から1mmほど逃げたところにフレームの端を揃え、曲がる部分もフレームを切り取ってあります。
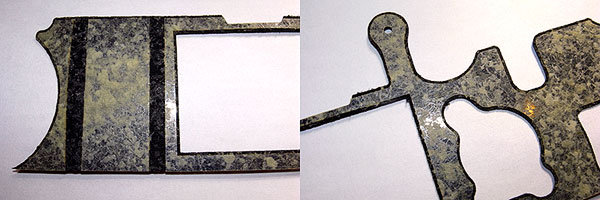
白っぽい汚いのは、エアーで吹き付けた接着剤です。
この裏革の作り方は、まずスエードとフレーム素材を貼り合わせて、レーザーでスエードとフレームの輪郭を切り出します(カットアウト)。次にレーザーの出力を弱めて、フレームが切れるだけのパワーで切っていきます(ハーフカット)。このパワーが微妙で、強すぎるとスエードまで切れてしまって意味がありませんし、弱すぎるとフレームがカットアウトせず、意味がありません。
データさえ決まってしまえば、一工程で加工機が勝手にやってくれますので、楽な作業ではあります。
ハンドメイドでは出来ない緻密な作業です。人間には出来ない作業を機械にやらせるという力業と言えるかもしれません。
ケース製作は動画を撮りましたので、ご興味のある方はぜひご覧ください。
刃型の製作を含むケース製作の一例(Canon Demi EE17用ケース)
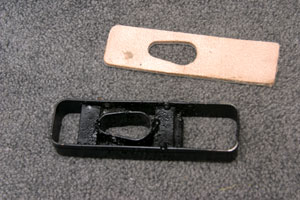
始業8時。まず底部の刃型から曲げ始め、8時30分に底部の刃型完成。
底部の形は変わりませんから、初めから刃型を作っておきます。
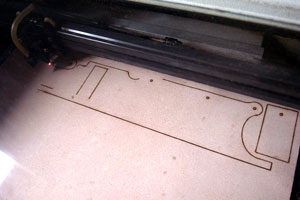
製品になる厚みと同じ厚みに合わせた床革を用意して、8時45分からひたすらレーザーを稼働してカット→CADでデータを直して、さらにカットしてケースを組み上げて、データ直してと延々繰り返します。

11時半時点でプロトタイプ13号。ほぼ形が決まりました。あと2つ試作を進めて、プロトタイプ15号で、形は決定いたしました。ここで一旦昼食。
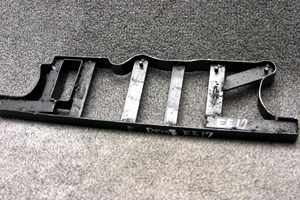
12時から側面の刃型を曲げ開始。13時に側面刃型完成。
意外と問題なくすんなり曲がりましたが、ここで溶接棒(半自動溶接機ですので、棒ではなくワイヤーですが)が無くなり、ホームセンターに買いに行く羽目になりました。
さらに溶接機の部品が壊れていることを発見して再度ホームセンターに走ります。これで2時間ロスしました。
15時頃から再度トップに回すベルト部分の刃型+側面の別パーツ部分の刃型曲げ開始。
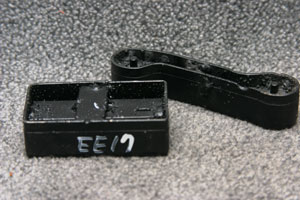
溶接機のアークの飛びが悪く、いつもよりもさらに汚い溶接となってしまいました。
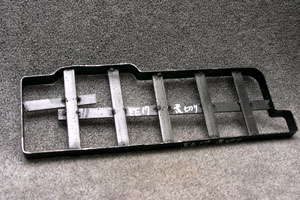
17時頃から荒切り用の刃型曲げ。そして刃型にポンチを入れ(これが面倒)、さび止めの塗装で、だいたい18時半頃、刃型はすべて完成。
19時頃から出来た刃型を使って縫製開始。
19時45分頃、とりあえず縫製終了。
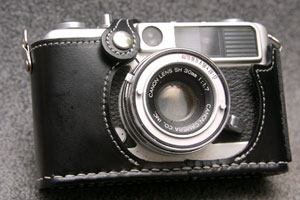
完成品の大きな画像は受けのイメージをクリックしてご覧ください。
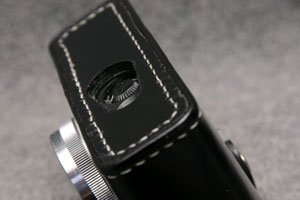
今回工夫したポイントは、側面と底部の合わせ部分は縁返しをして高級感をアップ。切りっぱなしと比べて丸みが出て、さらに製品らしくなります。
何とか一日で完成いたしました。途中の2時間ロスタイム以外は、すべての面で相当運が良かったです。
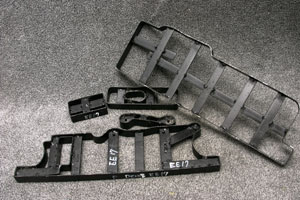
出来上がった刃型群です。
荒切り用、底用、サイドパーツ用、軍艦を通すベルト用、側面用、合計5点。
外注するとおそらく3万〜4万円。自分で作れば実働4時間〜5時間。プロが曲げた方が精度が高く綺麗であることを考えたら、外注の方が長い目で見れば安いと言えるかもしれません。
|